02.14
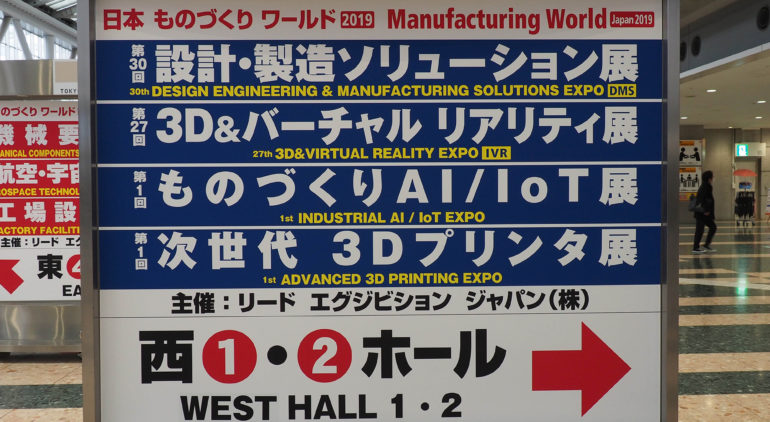
【World MR News】ホンダの開発プロセス改革に向けたVR/MR技術の活用――「3D&バーチャル リアリティ展」レポート③
2月5日から7日まで、東京ビッグサイトで最新の3D技術や超高精細の映像技術が一堂に会した展示会「3D&バーチャル リアリティ展(IVR)」が開催された。本稿ではその中から、2月6日に行われた本田技術研究所 四輪R&Dセンター デジタル開発推進室 CIS2ブロック 研究員 田中靖己氏によるセッション「VR/MR活用 開発プロセス改革 ホンダの開発プロセス改革に向けたVR/MR技術の活用」の模様を抜粋してお届けする。
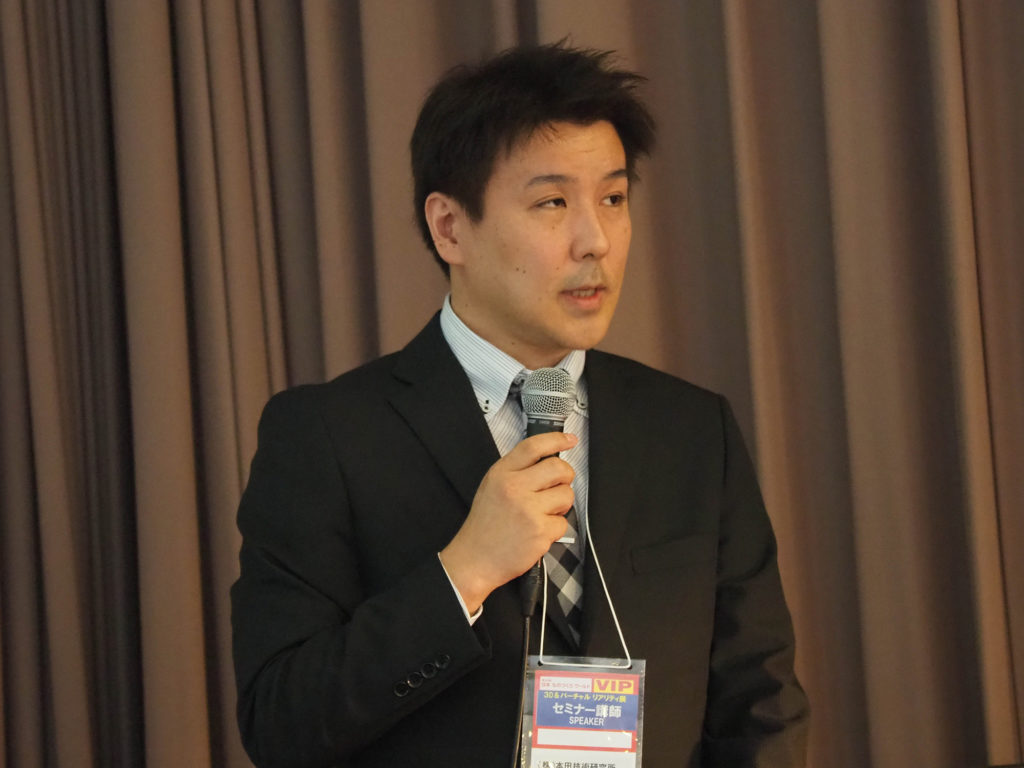
本田技術研究所の田中靖己氏。
ホンダの設計者を取り巻く開発環境が大きく変化
1946年に本田宗一郎氏によって創業された、ホンダ。オートバイから自動車、航空機など日本を代表する輸送機器及び機械工業メーカーである。1960年より、本田技研工業より分離する形で本田技術研究所が誕生。主に本田技研工業が販売と生産を担当し、開発を本田技術研究所が担うという形で役割が分担されている。
中でも四輪研究所は海外展開も行われており、全世界で26もの拠点が存在している。研究開発としての役割はふたつあり、将来的に商品として具現化したい新技術の研究を行う「要素研究(Research → R研究)」と、魅力のある商品を開発する「商品開発(Development → D開発)」だ。
田中氏によると、同社の設計者を取り巻く開発環境は大きく変化してきているという。昔はあくまでも実車を中心とした開発がメインであった。そのため時間は掛かってしまっていたが、全員で全体を理解しながら最適解を追求してきた。
しかし、デジタル化が大きく進んだ現在ではその状況も変わってきている。設計側と「人間工学」「騒動・騒音」「衝突」といったそれぞれのCAE(コンピューターで解析)担当者との間は、3Dデータとそこから絞り込んだ結果情報のやりとりで分担されている。各担当者はその領域だけを見ているため、横の繋がりが薄く製品の複雑化とCAEの専門性が深化している。そのため、多角的な視点で開発設計を行うことが難しくなってきているという。
設計者を取り巻くシステムも、やはりCADが中心となっている。そこにVRも加わり可視化・共有化を目的とした新たなプラットフォームに進化している。このVRに関しては、昔やっていた作業をVRで実現しようとしているという。同社ではそれを「VE:Virtual Engineering」と呼んでおり、設計者、開発リーダー、テスト担当、品質部門、製造部門が、それぞれが可視化・共有できるようにしている。
開発プロセスでのVR・MRを活用
以前は「外観品質検証」や「HMI」といった構想段階や研究制度の向上に係わる部分は、実車やモックを使って行われていた。また、「車体組付性検証」も昔は実機が使われていたという。しかしこれらは、5年前からVRやMRが活用されており効果が出てきている。
■外観品質検証
「外観品質検証」は、設計者が設計外観データに係わる部分に関して、ユーザー視点で外観商品性の向上を図って量産に繋げることを木艇に行われるものだ。その検証として使われているのがVR検証である。
その結果、設計者が試作車を作成する前に不具合改善につながる確認ができるようになり、商品性が向上している。また、外観確認をするための試作車も不要となったそうだ。ちなみに、この外観品質検証を行うための、専用の部屋も同社では用意している。
■HMI
「HMI」とは、ヒューマン・マシン・インターフェイス(人間工学)のことを指しており、視界性の検証のために実施されているものだ。ボディ設計、エクステリア設計、インテリア設計、ドア設計、衝突安全、エアバッグ設計、スタイリングデザイン(エクステリアとインテリア)などがそれらに該当する部分である。
その目的は、デザイン提案をベースに良好な視界と高い使い勝手の両立を図ることだ。こちらもVR検証が検証方法として採用されているが、「外観品質検証」のほうは2Dも活用されているのに対し、こちらは基本的に3Dで行われている。
その効果として、早い段階からブラッシュアップができるようになり、デザインや視界性を両立した車両開発が可能になったという。たとえば、コーナリング時の視界については、以前はCADで検証していたということもあり、いわば紙芝居風であった。しかし現在はVRを活用しているため動的に確認できるようになっている。
■車体組付性検証
「車体組付性検証」は、開発初期段階に組み付け生技性を検証して、実機を制作するときの手戻りを防ぐために行われるものだ。こちらは実際に組み立てることができるか、VRを使って検証を行っている。
組み立ての作業従事者が、VR環境を使ってデジタルモックを組み立て順に従って組み立て作業を行い、作業性の不具合を見つけていくという感じである。
ドアガラス組付性検証では、以前はCADでひと月掛かっていた作業が、VRを活用することで5分にまで短縮できるようになった。また、3Dメガネを通して見ることができるので、実車のよう確認できるようになったという。さらには、動画の再生も行えるため、熟練者の奇跡を新人が見られるというメリットも生まれている。
こうしたことから、現場から上がってくる声は好評で、操作が覚えやすいといった意見があった。不満や要望としては、ガタツキの再現が行えるようにして欲しいということや、VR酔いという点が上げられていた。
■手入れ性検証
「手入れ性検証」は、試作車レス開発に向けて、開発初期段階の生技性領域不具合を打ち上げることで品質向上を目指すために行われるものだ。以前は実機で手入れをして検証を行っていた。こちらも現在はVR検証が行われている。部品を持つ手を加えてVR環境で組み立て作業を行い、手入れ性を含めた作業性の不具合を確認している。
こちらの印象としては、「目線や手の認識がリアルで持つ感覚がイメージしやすい」や「CADの検証より早い」という意見が出ていた。また、要望や不満点としては、つまむ再現がしたいなどがあったという。
VRを利用することで車体組付性検証の効果は、確認・判断の精度の両方に効果があり、90パーセントも効率が向上したという結果が出たそうだ。
MR技術が「作業段取りプロセス改善」につながるか検証
同社では、開発全体の効率を向上させるための試作として、MR技術を活用して車体制作時の段取り時間の短縮を図るという試みが行われている。
従来までは品質確認は、2Dの紙図面と3Dの実車で見比べながら作業が行われていた。しかし、それらは『HoloLens』などで確認できるのではないかと考えたという。また、実車がない状態では、ロボットにティーチングが行うことができなかった。こちらも、CADデータがあればロボットにティーチングが行えるのではないかと考えた。MRで20パーセント、実機ロボットティーチングで30パーセント、トータルで25パーセント短縮できるのではないかと想定し、その検証が行われている。
検証技術の対象となったのは、『HoloLens』や『Meta2』『Magic Leap』といった「光学シースルー」デバイスと、『MREAL』などの「ビデオシースルー」。そしてスマートフォンなどの「スマートデバイス」だ。「光学シースルー」のメリットは手軽に利用できるところで、デメリットは現実とCGの焦点不一致だ。「ビデオシースルー」のメリットは、現実とCGが一致するところで、デメリットは画像遅延である。
MRの可能性を確認する「技術可能性」では、「ビデオシースルーHMD」が描写性、位置精度、作業性、総合評価のいずれも高評価だったが、一応いずれも使えることがわかった。また、スマートフォンも当初思っていたよりも良かったという。
描画性の検証では、スマートフォンはゴーグルを付けていないため逆に遠近感が掴みやすかったという。また、奥行きに関しては「ビデオシースルーHMD」が高評価だった。現実とデータ誤差を表す位置精度では、品質とティーチングのどちらとも「ビデオシースルーHMD」が高評価であった。
こうした検証の結果、選ばれたのは「スマートデバイス」であったという。「ビデオシースルーHMD」に関しては、その重さがネックになっているということもあり継続検証となっている。また、今回の検証で一番評価が低かった「光学シースルーHMD」については、新バージョン待ちという結果になっている。
これらのXRデバイスは日進月歩で進化を遂げているため、今後も新たなデバイスが登場していくことで、こうした開発の環境も大きく様変わりしていくかもしれない。
Photo&Words 高島おしゃむ
コンピュータホビー雑誌「ログイン」の編集者を経て、1999年よりフリーに。
雑紙の執筆や、ドリームキャスト用のポータルサイト「イサオ マガジン トゥデイ」の
企画・運用等に携わる。
その後、ドワンゴでモバイルサイトの企画・運営等を経て、2014年より再びフリーで活動中。